News
HortiDaily: Semi-closed greenhouse next step for innovative lettuce growers
cooling facility and water-cooled lamps
They were amongst the first growers to work with LED lights, incorporated a very innovative way of growing lettuce on water and are specialised in growing different lettuce varieties. Now Arjan & Leonard Boer of BoerDenHoedt are ready for the next step. Under the brand-new company name FromBoer, they will build a 4 ha semi-closed greenhouse in the South of Netherlands. Equipped with cooling facilities and water-cooled LED-lights, this will surely be the coolest greenhouse to be realised in the Netherlands, this year
Over 40 years of growing
The family business started in 1968, when mr Boer Senior started growing cauliflower, spinach, Chinese cabbage and other vegetables, in a cold greenhouse. Ever since the start of this century, they specialised in growing lettuce, and throughout the years they specialised in growing special lettuce varieties. The greenhouse that was built for this in 2005 shows the innovative character of the company: on a mobile gutter system, lettuce is being cultivated year-round. Four years later, they were the first lettuce growers to start working with water-cooled LED grow lights by Oreon.
Due to the development of a new business park, the company had to be relocated and they found their new location in Dinteloord, in the south of Netherlands. "In Dinteloord, we were welcomed with open arms," says Arjan. "Here we can expand to 6 hectares," adds his brother Leonard. They also took the opportunity to rename their company and the venture will continue as FromBoer - a name with a double meaning, since their last name coincidentally means 'farmer' in Dutch. "The new name suits the increasing internationalization of the company and the growing importance that consumers attach to the origin of the product,” they explain.
Connecting with the consumer has become increasingly relevant to the growers. FromBoer wants consumers to know that lettuce is more than a side dish or a summer salad. That's why they are collaborating with bloggers to show the versatility of the product - something they also did back in 2018, when they introduced their Lollo Bionda ice-cream.
Semi-closed greenhouse
Now the company is expanding. They're building a 4 hectares greenhouse in the South of Netherlands, with the opportunity to expand it to 6 hectares. The new greenhouse will be a semi-closed one. A Ulra Clima, to be more precise, built by Kubo. "The greenhouse is a combination of technology and high-quality innovation, whereby sustainability is paramount. It combines all the requirements that are demanded of a modern greenhouse. Higher production, maximum food safety, minimal energy and water consumption, minimal CO2 emissions and a better ROI. Additionally, the greenhouse will be equipped with energy screens." the lettuce growers point out.
Reusing heath from the LED lamps
And there's more coolness to be found in the new venture. As said, the growers were the first lettuce growers to opt for water-cooled LED lights, an innovation by the Dutch company Oreon. Now, they will also be the first growers to opt for the newest Oreon fixture: Monarch.
"In the current greenhouse in Ridderkerk, we have been utilizing Oreon's LED lighting since 2010. Actually, they have grown with us. We've done every expansion in LED lighting with Oreon, and we're happy to continue our collaboration in Dinteloord", says Leonard. "The new fixture comes just in time".
"The Monarch is compact, efficient and with 3100 uMol/s it has a very high light output. As a result, we don't have to hang as many lamps, we have less shade in the greenhouse, and lower costs", Arjan Boer adds. "The Monarch is efficient and is cooled with water. This keeps the lamps cool, which contributes to a long lifespan and a stable greenhouse climate. The heat dissipated from the lamps is reused, which also contributes to optimal energy consumption. All in all, it matches our sustainability goals completely."
No wonder Jan Mol, sales director with Oreon, is proud of his customers of the first hour. "The steps they take contribute to a higher return within their company and to a more sustainable horticultural industry, which benefits the entire sector. I greatly appreciate our collaboration and we're of course very proud that, shortly after the introduction of our new 'Dutch Powerhouse', we can contribute to their success."
Energy continuity
It might be clear: It's quite a cool, but also a complicated greenhouse that is being constructed. The facility will be equipped with many techniques the growers have used or tested over the last decades, for example with a growth cell, different lighting spectra and air treatment.
Also, the greenhouse will be equipped with a central energy supply (their own gas line and their own electricity station). "This ensures continuity in energy. And in the future, our energy supply will become even more sustainable because we will be able to use residual heat from the nearby sugar beet processor."
In order to fit them all in, they teamed up with consultancy firm Vyverberg, a company with extensive expertise in the horticultural industry, which helped them to realise all their wishes in the new facility. Supported by the consultants of Vyverberg, they found the optimum way of implementing these techniques in their new facility. Together, they created a Requirement Program that combined the ideal climatic circumstances with the availability of energy, the logistic requirements, and, all in all, the total feasibility of the project.
For example, over the last couple of years, the growers have learned that lettuce benefits greatly from cooling the greenhouse. "Now they would want to be able to heat and cool the greenhouse with the same system", Huib Herbert with Vyverberg explains. "By designing an air-treated greenhouse and fitting a heat pump, this turned out to be possible."
It's an example on how all the various techniques are implemented into the same system. "As soon as all the building blocks for this project were known, we started connecting the different suppliers. By involving these parties in the project at an early stage, the installations are coordinated in advance, resulting in a complete growing facility."
Click here to read the article on HortiDaily.
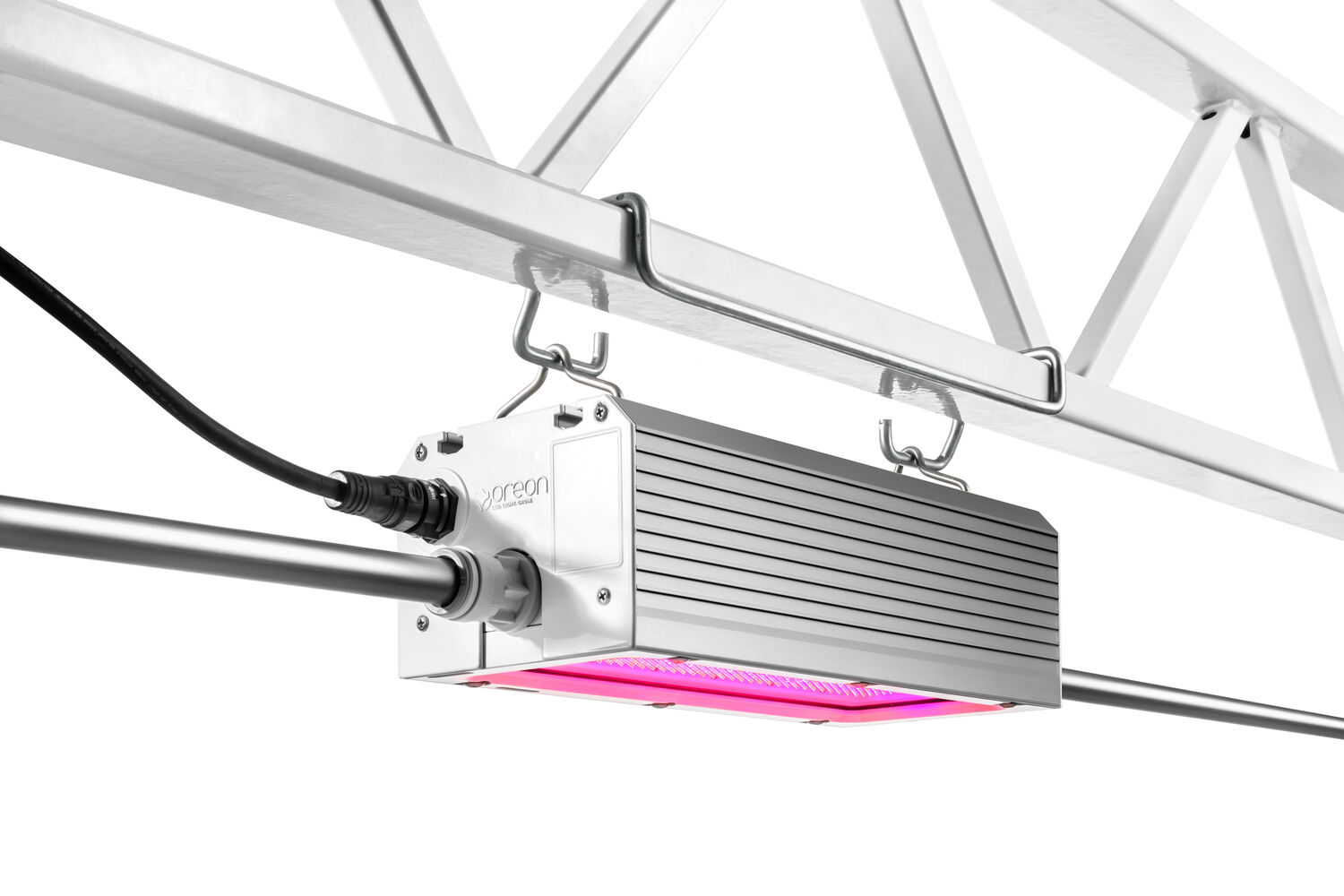
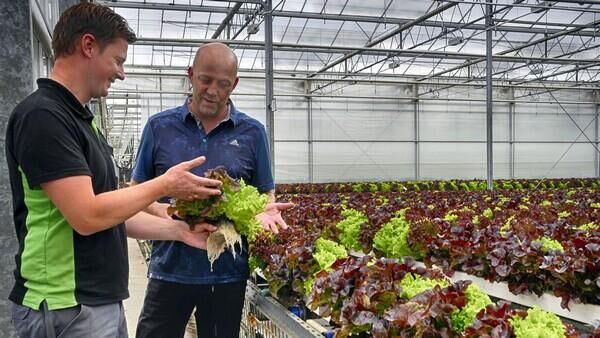
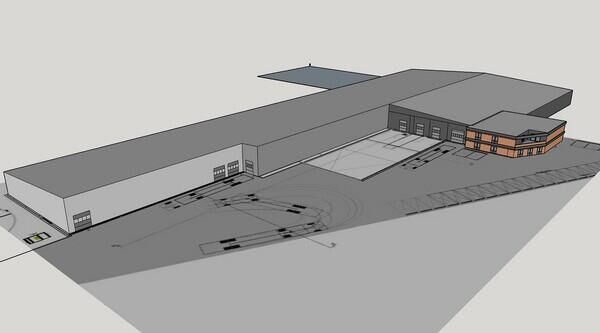
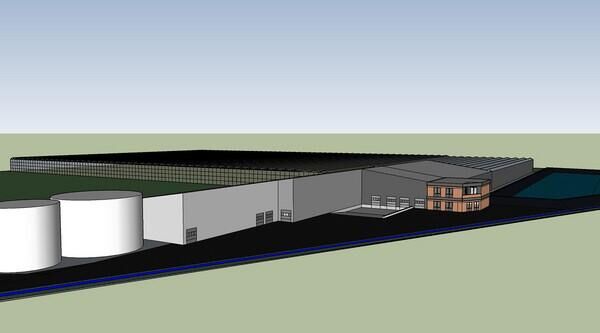